The Two-Shot Injection Moulding Method Explained
- gapprocomplastics
- Mar 6, 2023
- 4 min read
Updated: Jul 10, 2023
Nowadays, several businesses provide one- or two-shot technical injection moulding as a specialisation. If you are searching for a company that provides this service, make sure you choose one that has established itself as a market leader in the industry with regard to the technical elements of the process of injection moulding. Having the knowledge and expertise necessary for the complexity of two-shot mouldings.
What exactly is a two-shot injection moulding process?
The technique of injecting two different polymers during a single cycle of the injection moulding process is referred to as two-shot injection moulding.
During two-shot moulding, a polymer substrate is injected first. Next, a second polymer shot is moulded on top of the substrate and adheres to it. The rapid succession of shots allows the polymers to chemically bind as if they were one and the same substance, creating a strong bond.
Why go with a two-shot moulding instead?
There are many benefits to using two-shot moulding rather than over-moulding or manually installing single-shot components:
Enhancement of the aesthetic value of a single component that is flawless
Quicker turnaround times in manufacturing
Cost savings across all subsystems
Improved product toughness as a result of the chemical bonds between polymers being so strong.
Makes it possible to combine many functions, such as buttons and windows, into a single watertight unit.
How does the two-shot system function?
In over-moulding, a second polymer is moulded on top of the first one using a separate set of tools. On the other hand, in two-shot moulding, both polymers are shaped using a single set of moulds.
To form the basic shape of a product, a first polymer (the substrate) is injected into a first-shot tool cavity. When the first shot is retained throughout the mold's separation and rotation, the tool's second cavity is brought into alignment with the first shot before the mould is closed. It is over the top of the substrate that the second polymer is injected into the second-shot cavity. When the moulding has been completed, the tool is spun back 180 degrees to its initial position. Next, the finished moulding is pushed off the tool.
The process also aims to achieve different textures and colours
Two-shot moulding allows for the use of several polymers to create a product with a wide range of colours, finishes, and textures. Two-shot moulding is often used to create products with a rubbery feel for improved grip by mixing a hard plastic (the substrate) with a softer plastic (the overmold). The rigidity and contours of the product come from the harder polymer, while the improved use and visual appeal come from the softer polymer.
Windows and buttons are two other common applications for two-shot moulding. Two-shot injection moulding allows for the insertion of windows or buttons as part of a single watertight component. And this is as opposed to moulding the pieces separately and merging them manually using seals or a later over-molding process.
These autoinjector casings for clients are a great example of a two-shot component. Both shots are made from the same polymer. However, the first one is transparent, and the second one is coloured. This design makes use of a variety of colours to make the process of determining the potency of the medicine considerably faster. As a result, consumers feel more secure knowing that they selected the appropriate vial. Injection moulding using a two-shot process is widely used in the healthcare and medical sectors.

Two-Shot Molding Tool Development
Two-shot moulding is more complicated than single-shot moulding, which means the tooling required to produce the parts must be more intricate. In addition to the myriad of design concerns that are involved in the creation of any mould tool, such as the following:
The contours and proportions of the product.
The number of individual components that will be manufactured.
The temperature of the tool
The surface's finishing.
When working with two-shot tools, there are several extra mechanical concerns that need to be taken into account to achieve exact cavity alignment.
Tool design is heavily influenced by the choice of materials. There is a wide variety of materials available, and each has its own set of advantages and disadvantages. While making the tool, it's important to keep in mind that various polymers have varying shrinkage rates, cooling times, and flow behaviours. The interaction between the two polymers and the strength of their binding together should also be taken into account when selecting materials for two-shot moulding.
Two-shot moulding machine setup
If you're using a single-shot injection moulding machine, you simply need one hopper of material and one feed point. Two-shot injection moulding, on the other hand, needs not one but two feed points, each with its own hopper. And this is to ensure that both injections come out perfectly. Often, the feed points are set at right angles to one another. This also allows for a unique perspective on both the first and second shots.
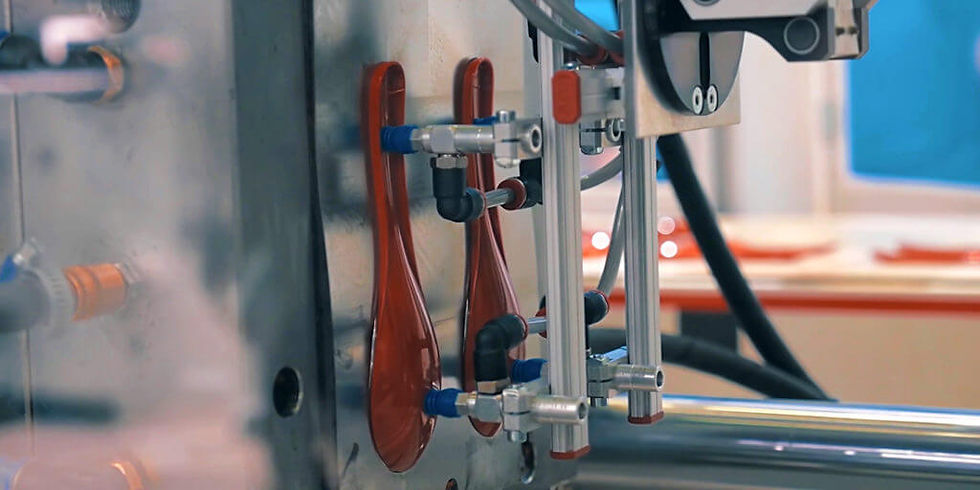
The importance of hiring a trustworthy injection moulding provider
Your goal should be to locate a company that can serve as more than simply a manufacturing partner. They should make it their goal to create value throughout the whole process of working on your project, from the planning stages through the production phase. They should also have extensive knowledge in single-shot and over-moulding in addition to two-shot moulding. Because of its comprehensive knowledge and competence in all aspects of injection moulding, this particular company can guarantee that not only will your product be optimised for manufacturing.
The cost should also be a factor to consider. As well as the benefits explained, the initial cost of the process can be a downside. However, the return on investment would be much greater in the long run.
Kommentarer